The 8-Second Trick For Alcast Company
The 8-Second Trick For Alcast Company
Blog Article
The Greatest Guide To Alcast Company
Table of Contents10 Easy Facts About Alcast Company ExplainedThe Best Guide To Alcast CompanyAlcast Company for DummiesThe Buzz on Alcast CompanyThe Best Guide To Alcast CompanyEverything about Alcast Company
Chemical Contrast of Cast Light weight aluminum Alloys Silicon advertises castability by minimizing the alloy's melting temperature and enhancing fluidness throughout spreading. Furthermore, silicon adds to the alloy's stamina and put on resistance, making it important in applications where durability is vital, such as automotive components and engine elements.It likewise boosts the machinability of the alloy, making it simpler to refine right into completed items. In this way, iron adds to the total workability of light weight aluminum alloys. Copper increases electrical conductivity, making it useful in electrical applications. It likewise boosts corrosion resistance and contributes to the alloy's general strength.
Manganese adds to the stamina of aluminum alloys and enhances workability (aluminum casting manufacturer). It is typically made use of in functioned light weight aluminum items like sheets, extrusions, and accounts. The existence of manganese aids in the alloy's formability and resistance to breaking during fabrication procedures. Magnesium is a light-weight aspect that supplies strength and impact resistance to light weight aluminum alloys.
The 10-Minute Rule for Alcast Company
It allows the production of light-weight parts with excellent mechanical residential properties. Zinc boosts the castability of light weight aluminum alloys and aids manage the solidification process during casting. It enhances the alloy's stamina and firmness. It is usually located in applications where intricate forms and great details are needed, such as attractive castings and specific automotive parts.
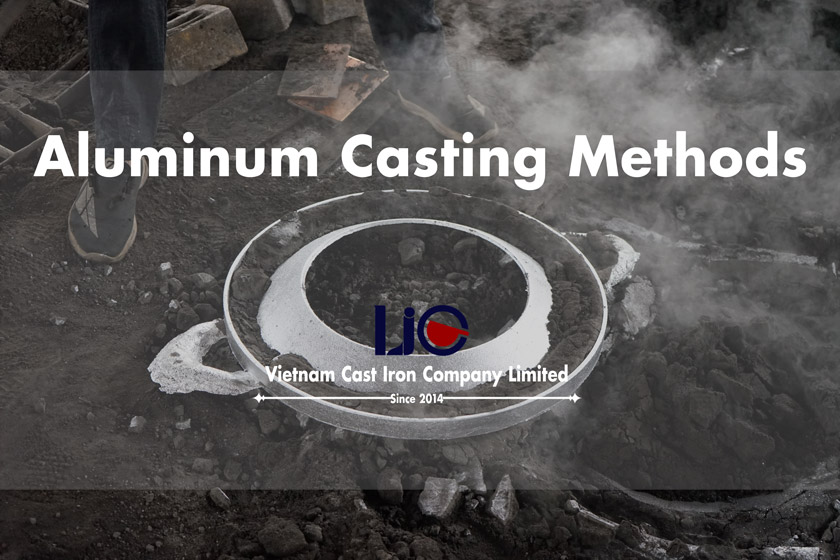
The key thermal conductivity, tensile strength, return strength, and prolongation vary. Select appropriate raw materials according to the performance of the target item generated. Amongst the above alloys, A356 has the highest possible thermal conductivity, and A380 and ADC12 have the most affordable. The tensile limitation is the contrary. A360 has the most effective yield strength and the greatest elongation price.
Alcast Company Fundamentals Explained
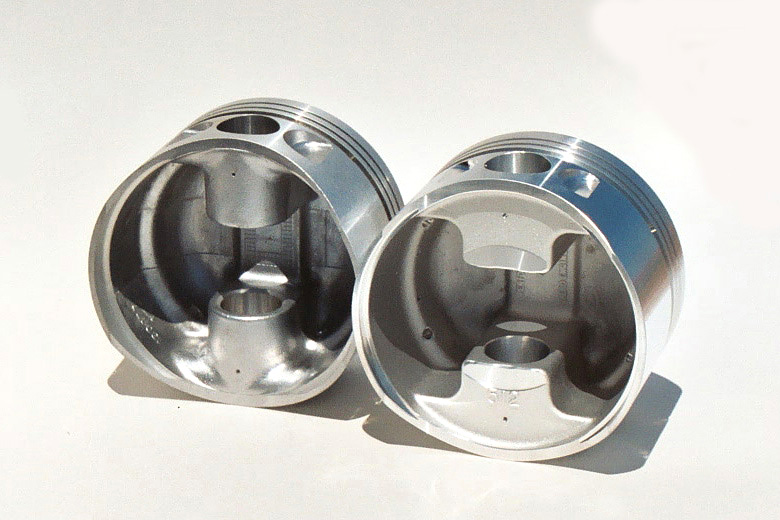
Its unique homes make A360 a beneficial selection for accuracy casting in these markets, improving product resilience and top quality. aluminum metal casting. Aluminum alloy 380, or A380, is a widely made use of casting alloy with numerous distinct characteristics.
In accuracy casting, light weight aluminum 413 shines in the Customer Electronics and Power Tools industries. It's commonly used to craft elaborate components like smartphone real estates, video camera bodies, and power device casings. Its precision is amazing, with tight tolerances up to 0.01 mm, making certain perfect product assembly. This alloy's superior deterioration resistance makes it an outstanding selection for exterior applications, making certain resilient, resilient products in the stated sectors.
Some Known Questions About Alcast Company.
When you have actually made a decision that the aluminum die casting procedure is suitable for your job, an essential following step is choosing the most suitable alloy. The aluminum alloy you pick will considerably influence both the spreading process and the buildings of the final product. Due to this, you have to make your choice very carefully and take an educated method.
Determining the most ideal light weight aluminum alloy for your application will certainly imply weighing a wide variety of features. The first group addresses alloy qualities that influence the manufacturing process.
8 Simple Techniques For Alcast Company
The alloy you choose for die spreading directly affects numerous aspects of the spreading procedure, like just how simple the alloy is to Discover More deal with and if it is vulnerable to casting problems. Warm breaking, additionally referred to as solidification breaking, is a typical die casting issue for light weight aluminum alloys that can lead to interior or surface-level tears or cracks.
Particular aluminum alloys are a lot more at risk to warm fracturing than others, and your option must consider this. It can harm both the cast and the die, so you should look for alloys with high anti-soldering properties.
Deterioration resistance, which is currently a noteworthy attribute of aluminum, can vary considerably from alloy to alloy and is an essential characteristic to think about depending on the environmental problems your item will be subjected to (aluminum metal casting). Put on resistance is another property typically sought in aluminum products and can distinguish some alloys
Report this page